The Internet of Things (IoT) is transforming various sectors, with manufacturing being one of the most significantly impacted. The integration of IoT in manufacturing is ushering in a new era of industrial innovation, enhancing efficiency, productivity, and profitability. This article delves into how the Internet of Things in manufacturing is reshaping the industry, its benefits, challenges, and future prospects.
Understanding the Internet of Things in Manufacturing
The Internet of Things refers to a network of interconnected devices that communicate and exchange data over the internet. In manufacturing, IoT encompasses a variety of devices, sensors, and systems that collect and transmit data to optimize operations. These devices range from simple sensors that monitor machine performance to complex systems that manage entire production lines.
The implementation of the Internet of Things in manufacturing involves embedding sensors in machinery and equipment, connecting them to a central system where data is aggregated, analyzed, and acted upon. This connectivity enables real-time monitoring and control, leading to smarter manufacturing processes.
Benefits of the Internet of Things in Manufacturing
1. Enhanced Operational Efficiency:
The Internet of Things in manufacturing significantly boosts operational efficiency by providing real-time data on machine performance, production processes, and supply chain operations. This data allows for predictive maintenance, reducing downtime and ensuring that machines are running at optimal efficiency.
2. Improved Product Quality:
IoT enables manufacturers to monitor product quality at every stage of production. Sensors can detect defects early, allowing for immediate corrective actions. This leads to higher-quality products and reduces the rate of rework and waste.
3. Cost Reduction:

The Internet of Things in manufacturing helps in identifying inefficiencies and waste, thus reducing operational costs. Energy management systems, for example, can optimize energy consumption, leading to significant cost savings.
4. Supply Chain Optimization:
IoT provides visibility into the supply chain, enabling manufacturers to track inventory levels, manage logistics, and ensure timely delivery of materials. This transparency helps in reducing delays and maintaining a smooth production flow.
5. Increased Safety:
Safety is paramount in manufacturing, and IoT plays a critical role in enhancing it. Sensors can monitor environmental conditions and machine health, alerting workers to potential hazards. This proactive approach reduces the risk of accidents and enhances workplace safety.
Data-Driven Decision Making:
The vast amount of data generated by IoT devices provides valuable insights for decision-making. Manufacturers can analyze trends, predict future needs, and make informed decisions that enhance productivity and competitiveness.
Challenges of Implementing the Internet of Things in Manufacturing
Despite its numerous benefits, the implementation of the Internet of Things in manufacturing comes with its set of challenges.
1. Security Concerns:
IoT devices are vulnerable to cyberattacks, and securing these devices is a major concern. Manufacturers need to implement robust cybersecurity measures to protect sensitive data and ensure the integrity of their operations.
2. Integration Issues:
Integrating IoT with existing systems can be complex and costly. Legacy systems may not be compatible with modern IoT technologies, requiring significant investments in upgrades and modifications.
3. Data Management:

The sheer volume of data generated by IoT devices can be overwhelming. Manufacturers need efficient data management systems to collect, store, and analyze this data effectively.
4. High Initial Investment:
The initial cost of implementing IoT solutions can be high, especially for small and medium-sized enterprises (SMEs). This includes the cost of sensors, connectivity, data storage, and analytics platforms.
5. Skill Gap:
The adoption of IoT in manufacturing requires a skilled workforce capable of managing and maintaining IoT systems. There is a need for ongoing training and development to bridge this skill gap.
Case Studies of the Internet of Things in Manufacturing
Several leading manufacturers have successfully implemented IoT solutions, showcasing the potential of the Internet of Things in manufacturing.
General Electric (GE):
GE has been at the forefront of adopting IoT in manufacturing through its Predix platform. This industrial internet platform collects data from machines and uses advanced analytics to predict equipment failures, optimize maintenance schedules, and improve operational efficiency. The result is reduced downtime and significant cost savings.
Siemens:
Siemens uses IoT to enhance its manufacturing processes with the MindSphere platform. This open IoT operating system connects products, plants, systems, and machines, enabling manufacturers to harness the power of data. Siemens has seen improvements in production efficiency and product quality, along with a reduction in energy consumption.
Bosch:
Bosch has integrated IoT into its manufacturing operations with the Bosch IoT Suite. This platform provides real-time monitoring and analytics, helping Bosch optimize its production processes. The company has achieved enhanced operational efficiency, reduced downtime, and improved product quality.
The Future of the Internet of Things in Manufacturing
The future of the Internet of Things in manufacturing is promising, with advancements in technology set to drive further innovation. Here are some trends to watch:
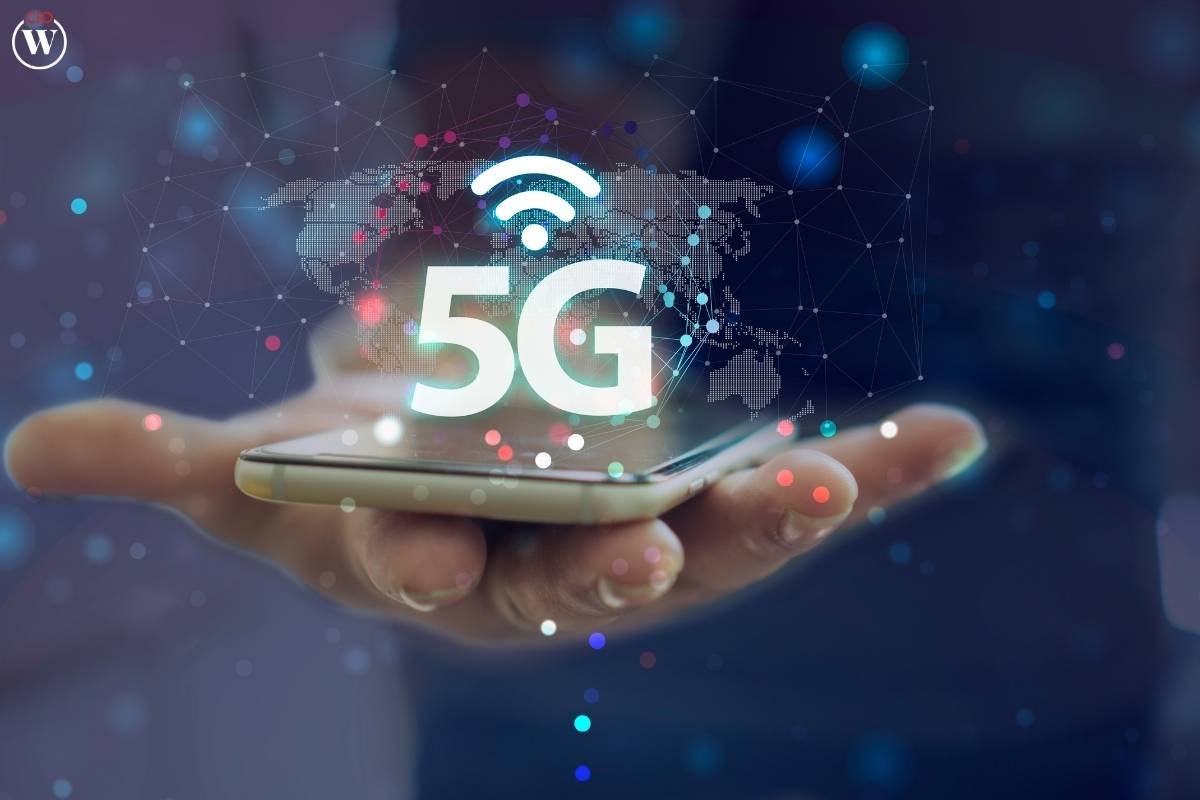
- 5G Connectivity: The rollout of 5G technology will enhance the capabilities of IoT in manufacturing. With faster and more reliable connectivity, manufacturers can implement more advanced IoT solutions, such as real-time remote control of machinery and enhanced augmented reality applications.
- Artificial Intelligence (AI) and Machine Learning (ML): The integration of AI and ML with IoT will enable manufacturers to derive deeper insights from data. Predictive analytics will become more accurate, leading to improved decision-making and further optimization of manufacturing processes.
- Digital Twins: Digital twins are virtual replicas of physical assets that use IoT data to simulate real-world conditions. In manufacturing, digital twins can be used to test new processes, predict maintenance needs, and optimize production lines, reducing the time and cost of development.
- Edge Computing: Edge computing involves processing data closer to where it is generated, reducing latency and improving real-time decision-making. For IoT in manufacturing, this means faster response times and enhanced reliability of critical systems.
- Sustainability Initiatives: IoT will play a crucial role in driving sustainability in manufacturing. By optimizing energy usage, reducing waste, and improving resource management, IoT can help manufacturers meet environmental regulations and reduce their carbon footprint.
Conclusion
The Internet of Things in manufacturing is revolutionizing the industry, providing unprecedented opportunities for efficiency, quality, and innovation. While there are challenges to overcome, the benefits far outweigh the drawbacks, making IoT a critical component of modern manufacturing. As technology continues to advance, the role of the Internet of Things in manufacturing will only grow, paving the way for a smarter, more connected, and more sustainable industrial future.